Excellent service, the highest quality and reliability - this is what distinguishes Weber Plastics Technology. How do we do it? Intelligent, cross-departmental processes. From the initial concept idea through to series production, project management works closely with our development, quality planning and industrial engineering departments. Over time, this close collaboration between departments has led to innovative and increasingly efficient processes that allow us to produce products of the highest quality with short lead times.
Project management
Working in parallel and worldwide standards make us a full-service supplier of the highest quality. We combine reliability, competence, planning and implementation with experience, professional expertise and a methodical approach across all our locations. By defining globally applied, goal-oriented standards, we reduce interfaces and sources of error. At Weber Plastics Technology, product ramp-ups are developed and improved continuously within working teams, so we always get the most out of our work.
Design
It's all a matter of design: Ambitious designs are becoming more and more important. It is not simply a matter of designing a product "beautifully". Rather, the challenge is to integrate functionality and ergonomics into product-specific shapes. Working with sensitivity and a trained eye, we combine construction, technology, economy, ecology and aesthetics to create a unique product fit for series production.
In order to meet our customers' individual needs, we work closely with them from the initial concept phase. This begins with research and analysis, and is followed by the elaboration of sketches of first ideas and CAD drafts, and finally goal-driven prototype construction. Following this working model not only brings first-class results; it guarantees production-oriented implementation.
Construction and development
We develop innovative solutions from plastic: With passion, expertise and a pioneering spirit. For us, working in close collaboration and constant dialogue with our customers is as self-evident as the demand we place on ourselves to always find the best solution. Our growing number of patented and patent pending products underlines this expertise.
We offer our customers:
- Pre-development to shape the automotive future
- Concept development for the realization of new components, modules and systems
- Series development
- Comprehensive simulation and analysis options, e.g. kinematics, FEM, lighting, acoustic analyses for the components, or mould filling analyses (rheology, temperature control) and assembly simulations
Rapid prototyping
Rapid prototyping greatly facilitates our development work, allowing us to identify problems at an early stage. By troubleshooting at such an early stage of development, we save on cost and time in later phases. We offer customers a rapid and economical production of prototype parts and installable modules. Our portfolio includes all common and necessary technologies, and is adapted to individual application.
Our range of services includes:
- Stereolithography (SLA)
- Laser-Sintering (SLS)
- 3D Printing
- Casts from silicone moulds
Mould management
We manage the project planning, procurement and qualification of all necessary injection moulds.
Our global supplier network offers customers economical solutions for every sort of application, while our management expertise means we can guarantee close support to this network. In this way we ensure that our customers receive their moulds promptly and in the required quality. In the procurement process we pay attention to both the quality of the mould and the safety of the injection moulding process, as well as to ease of maintenance.
With standardised procedures, wide-ranging personal experience and supporting simulation software such as mouldex 3d, for example, we achieve the target-oriented implementation of the development specifications.
Our mould-management system is backed up by our experienced and highly effective in-house mould maintenance and repair facility, which implements the necessary changes promptly and precisely.
Injection moulding
To ensure our injection moulded parts' top quality, we constantly modernise and improve our technical processes and monitor their quality online (CQC).
Depending on customer requirement, we use fully automatic, linked production islands. These include the process stages of injection moulding, surface decoration and assembly.
We employ the following manufacturing processes:
- Standard injection moulding
- 2- and 3-component injection moulding, e.g. for hard-soft moulded parts
- High-gloss injection moulding free of welding lines
- Plastic-metal-hybrid technology (with steel or aluminium inserts)
- Machine size 60-10, 800 kN
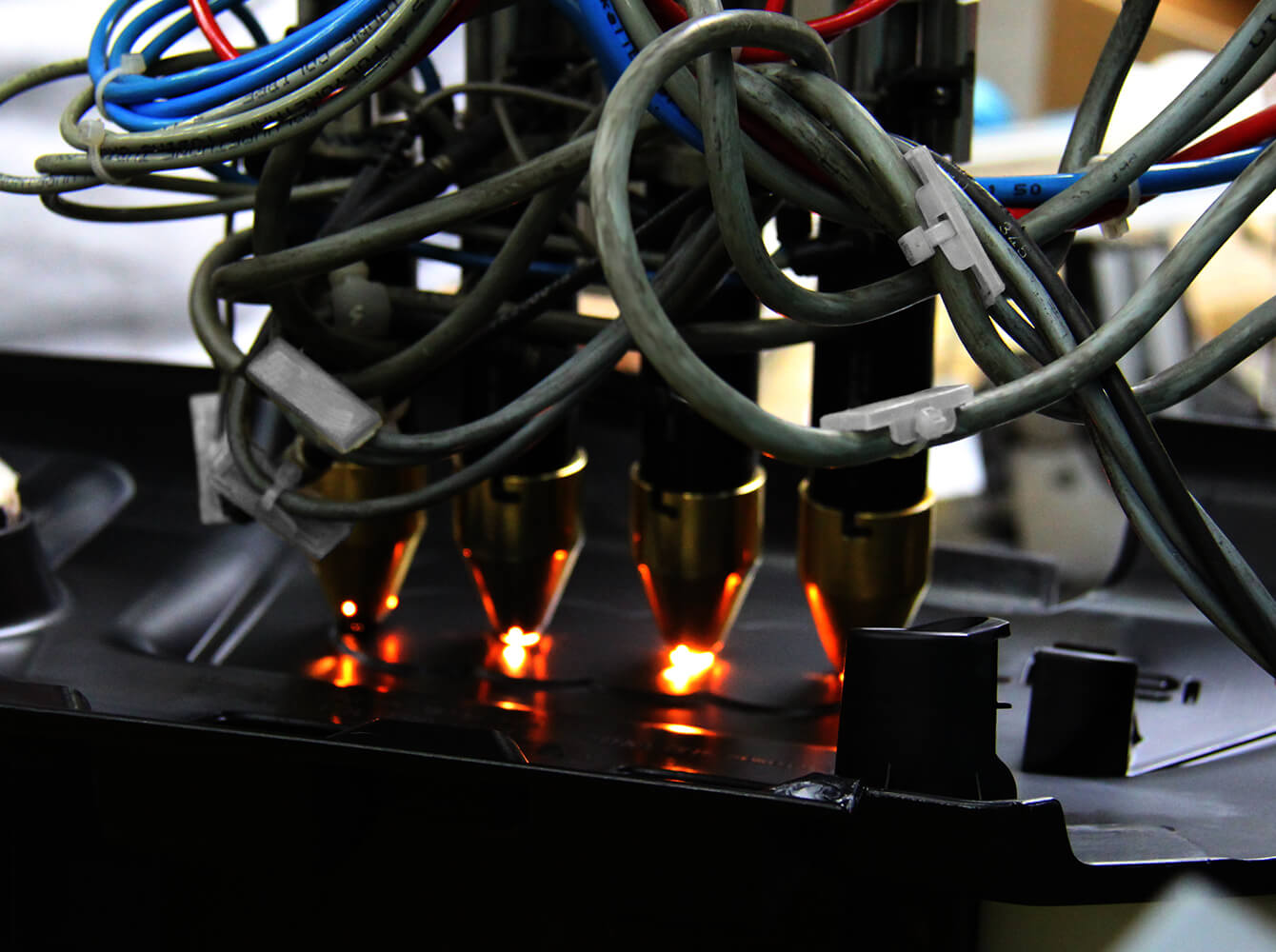
Joining technology
We offer effective and safe joining of plastic with plastic and plastic with other materials (e.g. metal). We always select the best procedure, ensuring smooth implementation. The various welding processes for plastics and foams we employ especially allow for individualised solutions. Increasingly, gluing is also used for our modules.
Welding process:
- Ultrasonic welding
- Heated tool welding
- Vibration welding
- Infrared Riveting
- Hot air riveting
Bonding method:
- Automated application of liquid adhesive
- Depending on the application, automated or manual application of adhesive tapes and pads
Assembly
We supply our customers with completely assembled, ready-to-install modules and systems. Working in close collaboration with our customers, we develop precisely fitting, efficient assembly processes. Depending on the application, assembly islands based on the "chaku-chaku" principle or fully automatic, linked production islands covering all process stages are used.
Examples within the automotive sector include ashtrays, cupholders, storage compartments and designed acoustic engine covers. Within the household sector, examples are table water filters or drinking bottles with integrated activated carbon filters.
Surface decoration
Attractively designed and high-quality decorated surfaces are increasingly important. Depending on design requirements and the field of application, our products are decorated through various processes.
We offer the following methods:
- Plastic chrome plating and chrome effect paints
- Pad and screen printing
- Decorative hot stamping
- Flocking
- Laser inscription
- Painting with water- and solvent-based paints
- In mould decoration, in mould labeling
This allows us to create a variety of visual and tactile impressions and give an individual touch to the products. As an expert in surface decoration, we develop solutions for a wide range of applications that match customer requirements completely.
Our ultra-modern painting plant allows for almost any type of painting, and can be flexibly adapted to the components that are to be coated. Special effect, haptic, decorative and high-gloss coatings can be applied to all common plastic substrates. The paints used are 1- or 2-component water or solvent based systems. A total of four programmable 6-axis robots are used to apply the paint layers, using 1- and 2-layer coating systems. The parts to be painted are first cleaned using a 4-zone Powerwash system, then - if necessary - a primer or basecoat is applied, followed by a top or clear coat. Components may also be partially painted.
Using a transponder control, we ensure complete traceability of the painted components throughout the fully automated painting process. The advantage: All relevant process parameters are recorded over the entire painting process and assigned to the component. Tracking the parts and the process parameters is thus possible over many years. What's more, our quality team covers all required testing. Our laboratory features its own testing facilities to perform various adhesion tests, abrasion and media resistance tests, air conditioning storage, colour and gloss level measurements, layer thickness measurements and microscopic examinations.